6 Ways to Improve Industrial Mixer Efficiency
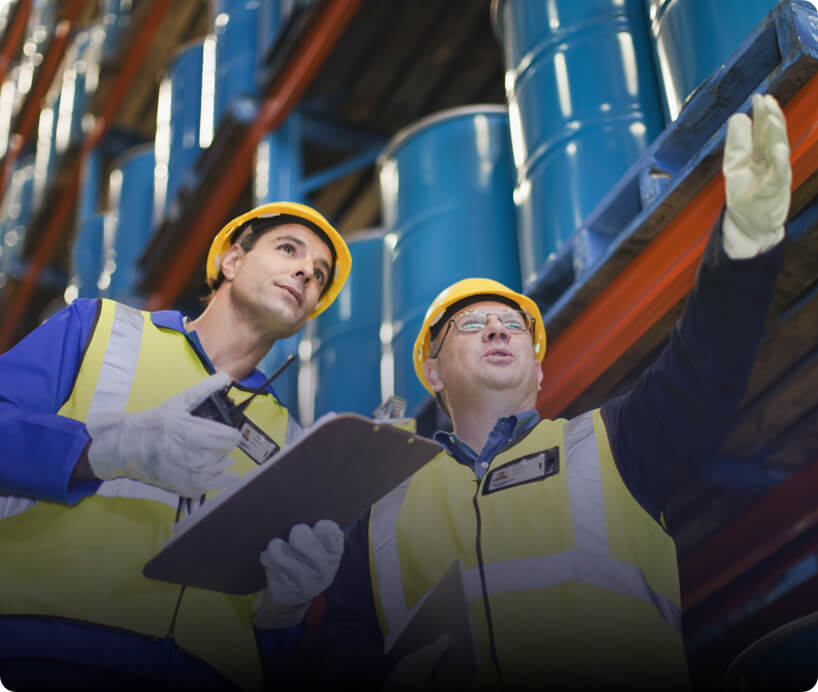
The COVID-19 pandemic has affected industries of all types globally, with many either slowing down considerably or halting completely in the interim. But, when we finally begin to return to some sense of “normal,” it’s anticipated that consumer demand will rapidly increase — and every industry should be prepared for that moment. One way to ensure production runs smoothly today — and tomorrow — is by focusing on industrial efficiency.
What is industrial efficiency? Simply defined, industrial efficiency is the ability of a manufacturer to produce a product with the minimum waste possible to maximize yield and therefore profit. Efficiency is critical to competing in any industry. For batch producers of mixed liquid products an efficient and properly sized mixing system can reduce material waste, direct labor, cycle time, energy and environmental impact — resulting in better product quality and customer satisfaction. So, what are some areas to focus on for improved industrial efficiency?
1. Reduce Waste: Seek to reduce waste in all forms; energy, materials, labor and exertion through optimal process flow and equipment selection.
2. Improve Training: A well-trained team can make or break a bottom line. Ensure that production specialists, including mixer operators, are given the equipment and information to operate machinery safely and correctly. Continue training for operational improvement as processes are developed with a focus on reduced operator travel, monitoring time and cleanup. INDCO has a large library of helpful documents and manuals available on our website.
3. Standardize Work Processes: Individuals have their own way of doing things, but in a manufacturing setting, precision is key for efficiency. Institute checklists, process documents or standard operating procedures (SOP’s) to ensure consistent results. The sequence of ingredient addition, for example, can have a huge impact on mixing times and therefore labor cost per batch.
4. Organize the Workspace: Excess movement across a manufacturing floor can end up costing a lot over time. Consider containing production into “cells” on the floor to reduce travel time by employees and keep process materials, ingredients and tools in close proximity wherever possible.
5. Commit to a Maintenance Schedule: Any machine can fail, but most failures are preceded by warning signs. Pay close attention to the sound of the mixer as it runs for changes, observe mixer rotation for vibration, and clean mixing equipment between batches. During cleaning check for changes in fit between mixer shafts and couplers or impellers to the shaft if removable. Create a routine maintenance schedule and checklist to avoid work stoppage and safeguard equipment health.
6. Focus on Equipment Design: Using the appropriate industrial mixer and related liquid handling equipment will help ensure output per unit of effort is maximized. One of the most inefficient mistakes is to utilize a mixing system for multiple applications for which it was not designed. While there are groups of liquid products with similar properties for which a shared mixer may produce acceptable results utilizing one that is not can create significant waste, especially if used for a high number of batches. The benefit from avoidance of acquisition cost can be much less than the eventual waste in extended batch cycle times, electricity costs, operator labor and monitoring time and maintenance. Always consult your mixing engineer to ensure the mixing system is optimized for the desired batch size or range of batch sizes.
From the viewpoint of industrial efficiency, larger units of production have impactful advantages over smaller units in both cost and output. That’s why choosing the correct industrial mixer for your industry is so important. Every industry — from pharmaceutical, food and beverage and cosmetics to construction — has its unique mixing system demands to provide the desired process outcome and to conform with operational and/or regulatory requirements.
That’s why, as the leading industrial mixer manufacturer, INDCO believes our diverse line of industrial mixers to be a valuable solution for the most efficient manufacturing goals. INDCO specializes in manufacturing industrial mixers for applications from laboratory scale to as large as 50,000 gallons and can be customized to fit any application needs. Our engineers use the mixer sizing worksheet to help clients determine the best equipment for their needs.
With our fast lead times, best-in-class raw materials and free engineering expertise, there’s a reason that when it comes to working with a variety of industries INDCO is always in the mix.
INDCO provides unparalleled quality with unparalleled care. To talk to a customer service representative about increasing your industrial mixer efficiency, or work with one of our engineers, visit our contact page today or call us at 1-800-851-1049.