Principles for High Viscosity Mixing
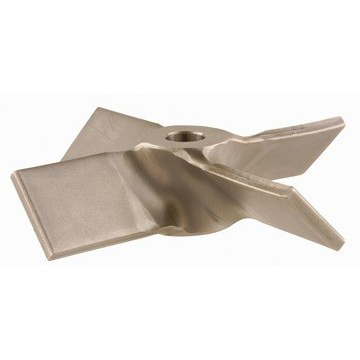
Liquid mixtures are produced for use in an extremely wide range of industries. What these formulations have in common is that they were mixed by mechanical means at some point in their production process. The majority of industrial mixing processes are low-viscosity fluids, i.e. those that move easily when agitated and continue to flow when agitation is removed. There is great flexibility in the design of mixing equipment for low-viscosity, or “water-like” products. High viscosity mixing, on the other hand, presents more challenges and requires some key principles to achieve. High viscosity mixing can generally be characterized as those formulations that do not “flow” easily, or perhaps not at all, unless directly driven by mechanical means. It is important to understand the differences between high viscosity mixers and high viscosity impellers versus those for low viscosities as incorrect selection will produce poor process results.
Mixing applications engineers configure mixers based on each project’s fluid properties such as density and viscosity. Of these properties, it is viscosity that describes to what degree a fluid resists movement. Viscosity can be measured in numerous different units but centipoise is perhaps the most common. While there is no single viscosity measurement that determines high viscosity mixing is needed it is generally chosen when analysis of the product’s flow is determined to need assistance to remain in motion. As viscosity increases the resulting flow is said to become more laminar than turbulent and this leads to mixer design characteristics that are appropriate for those conditions. While both low and high viscosity mixing applications can be common across industries some examples of successively higher viscosity mixing applications are as follows: blending of heavy paints or primers in the coatings industry, production of food products such as condiments and peanut butter, or finally, some printing inks can be among the most viscous of product formulations.
High viscosity mixing increases the importance of torque and mixing impeller type and diameter. High speed, direct drive motors providing rotational speeds over 1,000 rpm and a small mixing impeller will not successfully produce the pumping capacity or the flow pattern in the mixing vessel for adequate results. High viscosity mixers are characterized by being “gear-reduced” meaning that the mixer features a gearbox which reduces the rpm produced by the motor while greatly increasing the torque output. Since the torque is higher, the mixer shaft diameters are larger in order to drive impellers that may be sized at over 50% of the tank diameter to push the resistant liquid forward. Mixers for higher viscosities feature impeller types such as a three blade axial turbine or a four blade axial flow turbine which have broad blades with an aggressive pitch to maximize contact surface area during the mixing process.
INDCO provides standard mixers for processing high viscosity products for various container types. Our model DLG-1A, for example, is perfect for industrial grade use in open top 55-gallon drums. The STL-150T is designed for stainless steel totes and our MX-series of mixers is a floor-mounted lift mixer product line for mixing in containers from 1-gallon to 55-gallons or larger. For larger tanks our TM-series and FMG-series mixers are engineered to meet each application’s specific requirements.
Visit the INDCO website at www.indco.com to shop over 2000 industrial mixers and related products or call our friendly customer service representatives or applications engineers to determine your most effective high viscosity mixing solution at (800) 851-1049.