INDCO Industrial Mixing Design 101: A Basic System Design Guide
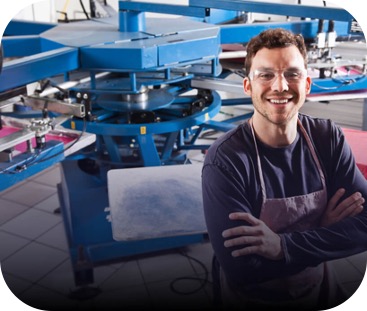
From inks and pigments to food and drug manufacturing, industrial mixing sustains daily production across industries. Despite how many hats industrial mixing wears, the basics remain the same. Most industrial mixing system applications involve blending low-viscosity liquids or liquids with soluble solid materials through the process of agitation. As viscosity increases or as less soluble material is utilized, applications become more challenging.
Each of these applications requires precise calculation and expertise to create a mixer comprised of the appropriate size for the intended capacity and the proper impeller to get the job done. Enter your trusted INDCO engineers who have been deploying this expertise and attention to details to create optimized industrial mixing solutions for decades. While analytical models may still be useful, the hands-on problem-solving of our team members helps to ensure that desired process results are achieved.
We know industrial mixing systems inside and out, and today, we are imparting some of that knowledge for the purpose of better understanding just how the mixing system design process works.
Get to know the basics.
An Overview of Basic Industrial Mixing System Designs
As with any technical topic, it’s always best to get started with some important definitions:
What is industrial mixing?
Mixing is defined as the intermingling of different materials (liquid, gas, solids) to produce a homogeneous mixture. Specifically, the best mixing occurs in the “zone of attrition,” or the highly turbulent region located at the impeller’s trailing edge. To ensure that a substance is properly mixed, the mixing system’s design must maximize the substance’s contact with the impeller.
What is material flow?
Material flow in mixing is the quantified liquid movement in the vessel as a result of impeller pumping capacity. Material flow pattern is the visualization of how and where the material gets moved throughout the vessel as it is mixed, and is influenced by the relationship between impeller and vessel dimensions, not simply by batch volume. A large impeller rotating slowly and a small impeller rotating quickly may have equal pumping capacities but will provide significantly different flow patterns.
INDCO engineers calculate pumping capacity in units, which include tank turns per minute, bulk fluid velocity, and agitation scale. Each impeller type (marine style impeller, hydrofoil, and axial flow turbine, to name a few) has a unique pumping number. Marine style propellers and hydrofoils are examples of high pumping impellers.
What is shear in mixing?
The technical definition of fluid shear is the change in velocity gradients along the profile of the impeller, or how much stress is applied to the mixed substance when it contacts the impeller. Shear rate is a characteristic of the impeller design or type. Shear stress, which provides fluid “micro-mixing,” stretching of liquid “particles” at the impeller, or dispersing of gas bubbles is the product of shear rate and fluid viscosity. Dispersion blades, homogenizers and rotor-stator designs are all examples of high shear mixers
All industrial mixing applications consist of a combination of flow and shear. The selection of impellers and speeds are made with this in mind, and their design is based on the desired properties of the final mixed product. The ideal mixing system design also includes vessel geometry, mechanical, electrical, and customer operating considerations. In short, there are many variables to consider when looking for an appropriate mixing system for your specific application!
Already familiar with the basics of mixing systems? Check out our series on stainless steel mixing tanks.
How INDCO Helps You Design an Industrial Mixing System
By utilizing some key information about your mixing applications and desired outcomes, INDCO customer service representatives and engineers can help you confidently design a successful mixing process.
The following is a list of important information to provide when working with us:
- Batch volume(s) including minimum and maximum desired batches, if applicable.
- Vessel dimensions (diameter, overall height, liquid depth) and geometry (flat bottom, cone bottom, etc.)
- Material properties
- Initial ingredient and final product viscosities
- “Water-like,” “similar to honey,” etc. can also be helpful
- Initial ingredient and final product viscosities
- Specific gravity or weight per gallon of ingredients
- Corrosive or flammable properties of ingredients
- Solubility of solids and concentration used
- Material properties
- Desired process outcome (blended liquid, solids suspension, etc.)
- Process description
- Sequence of ingredient addition
- Processes successfully used for small-scale or pilot batches
The Qualities of Effective Mixing System Design
The best industrial mixing equipment does not matter in the end without a carefully though, meticulous process behind it. What are some important qualities that go into the development of mixing systems? Essentially, this breaks down into 2 core components: theoretical design and practical design:
Theoretical Design
Using the information provided, INDCO personnel will first determine the optimal theoretical design, which includes the combination of impeller type, size, and speed in relationship to the vessel to provide the required material flow and flow pattern needed for the intended application. At this point, the required horsepower (motor size) and torque (gear reducer) are determined.
Role of the Reynolds Number:
Reynolds Number, in fluid dynamics, is defined as the ratio of a liquid’s dynamic to inertial viscosity in parallel planes under shear. More simply, it is an indication of how easily liquids flow or resist flow at the site of the impeller. Our engineers will calculate the mixing Reynolds number for your application to assist with the selection of impeller type and size. Low Reynolds numbers resulting from high viscosities generally require larger impellers to be paired with gearboxes for maximum surface area contact and increased torque.
Practical Design
Once the impeller type, horsepower, and torque that will provide the desired flow pattern and agitation are defined, the detailed mechanical design can then be created. Considerations that are necessary to complete this step include shaft length and diameter selection based on operating stress and critical speed avoidance. Critical speeds are rotational speeds at which natural frequency vibration is present. All rotating equipment has multiple critical speeds at which this vibration occurs. Mixer engineers calculate critical speeds based on the rigidity of the mounting method, the distance between support bearings, shaft length, and diameter and weight of the impeller(s). Industrial mixers are generally designed such that the operating range needed to provide the desired process result is not within 40% of a critical speed. It is common to quickly run a mixer through a first critical speed in order to reach the designed operating range.
Shaft and impeller material selection is based on the properties of the materials that are present in the mixture, and the most commonly used alloy for both shafts and impellers is 316 stainless steel. Final decisions to configuring the optimum mixing system include those relative to the production environment and the operational needs of customer personnel. If the available services permit it, air or electric motors may also be chosen. Gear reducers, if applicable, come in many configurations.
Options for motors and gear drives include finishes for indoor, outdoor, or sanitary wash-down industrial mixer applications.
Designing an Effective Industrial Mixing System with INDCO
Now that you have familiarized yourself with the basics of industrial mixing system design, it’s time to put that knowledge into action—and the team at INDCO is ready to work with you through the process. We offer hundreds of standard industrial mixer models, and each can be customized to your unique process requirements. We also provide a wide range of mixers, stirrers and dispersers for industrial mixing applications of up to approximately 5,000 gallons. Not sure where to begin? Our engineers are directly available to assist you with the selection of the industrial mixer or sanitary mixer that meets your requirements. Ready to get started? Contact us, or give us a call at (800) 851-1049. INDCO, Inc. is located at 4040 Earnings Way, New Albany, IN 47150.