Choosing Your Impeller
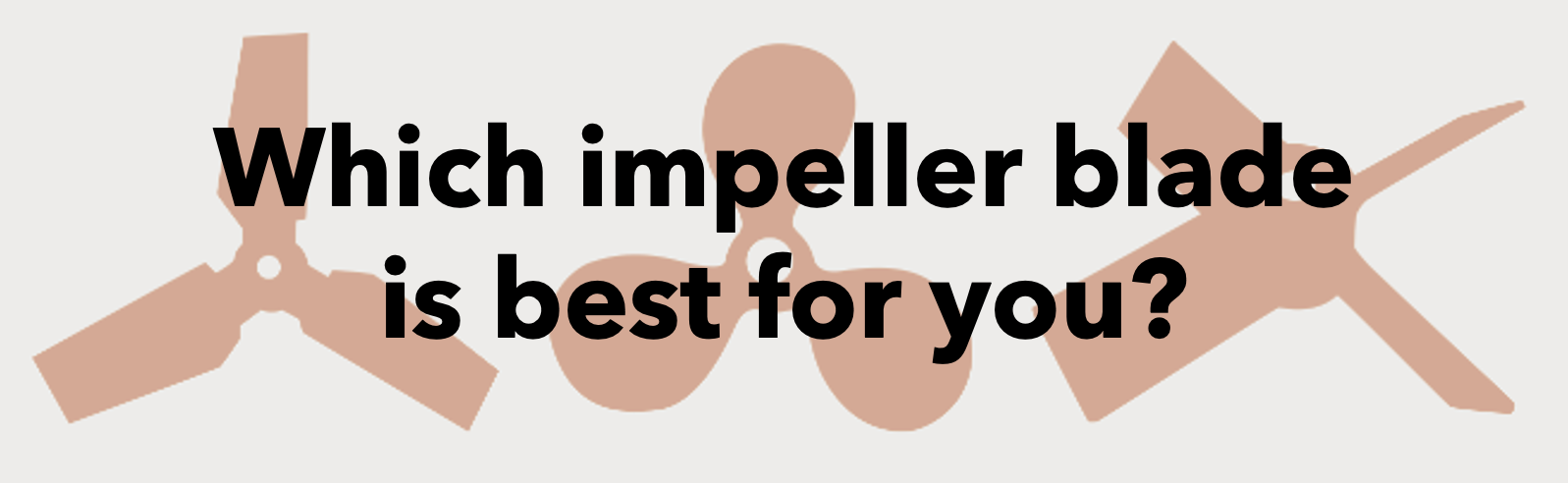
Considerations for Choosing Your Mixing Impeller
Choosing a mixing impeller is crucial for achieving the desired mixing results in industrial processes. First – what is an industrial mixing impeller? The impeller is the component responsible for imparting motion to the mixing fluid, which results in the desired mixing behavior. Several factors need to be considered when choosing an impeller, including the desired flow pattern, viscosity of the fluid, and the impeller's geometry.
The first factor to consider is the flow pattern which is where the fluid flows throughout the mixing tank. Different impellers produce different flow patterns, such as axial, or radial, each with their relevant applications. For instance, an axial flow impeller produces a vertical flow pattern parallel with the mixing shaft for a top mounted mixer which is suitable for the majority of liquid mixing applications. Radial flow impellers produce a horizontal flow pattern essentially pushing fluids outwardly away from the shaft and is commonly used in fermenting applications or as a bottom impeller when mixing very shallow batches in a large vessel.
The impeller's geometry, such as the blade's profile, width and angle, determines its ability to pump the fluid. While many impeller types will move low viscosity liquids a larger blade diameter, profile and more aggressive angle are required for mixing high viscosity fluids. Furthermore, mixtures requiring more “mixing action” or shear, may require an impeller with a more aggressive profile to produce a higher shear rate to ensure effective results. Finally, and very importantly, the impeller's size directly determines the power and torque required from the mixer drive system. A small incremental increase in mixing impeller size requires significantly more power to drive it. Therefore, always verify that the mixer motor and gearbox, if applicable, are adequate to prevent mechanical failure. Your Indco customer service representatives or engineers can assist with this.
The infographic below helps to demonstrate the differences between various INDCO mixing impellers.
Impeller types and their specifications:
- Hydrofoil Impellers
- Standard Diameter: 3' - 30"
- Batch Type: Low
- Options: Keyways, Metric Bores, Additional Set Screws, Polishing, and Electropolishing.
- Square Pitch Propellers
- Standard Diameter: 3' - 20'
- Batch Type: Low-Medium
- Options: Keyways, Clipping, Cutting, Pitch Changes, Metric Bores, Set Screws, Polishing, and Electropolishing.
- Steep Pitch Propellers
- Standard Diameter: 3" - 14"
- Batch Type: Low - Medium
- Options: Keyways, Metric Bores, Additional Set Screws, Polishing, and Electropolishing.
- Radial Flow Turbines
- Standard Diameter: 3" - 30"
- Batch Type: Low - Medium
- Options: Keyways, Metric Bores, Additional Set Screws, Polishing, and Electropolishing.
- Axial Flow Turbine
- Standard Diameter: 3" - 24" (3-blade), 3" - 48" (4-blade)
- Batch Type: High
- Options: Keyways, Metric Bores, Additional Set Screws, Polishing, and Electropolishing.