How to Operate an Electric High-Speed Disperser Mixer: A Basic Guide
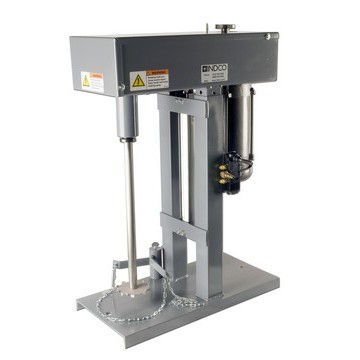
Whether you are new to using high speed dispersers or seek to expand your knowledge, we have you covered. We'll also answer some common questions about dispersers, their functionality, and their applications in various industries.
Understanding Dispersers
What is a Disperser Mixer Used For?
A disperser mixer, also known as a high-speed disperser mixer or high-shear disperser, is a powerful mixing tool used in a wide range of industries such as paints, coatings, adhesives, food and personal care products. Its primary purpose is to break down and disperse solid particles into a liquid medium, or to blend multiple liquids with different densities resulting in a homogeneous mixture.
The key difference between a flow-driven process, such as mixing miscible liquids with a marine style propeller and dispersion is that the dispersion process is shear-driven. The action from a disperser requires high speed with torque simultaneously. Therefore, it has more resemblance to the action in a kitchen blender than a stirring motion.
A Guide on Operating a Variable Speed Electric Benchtop Disperser
INDCO manufactures multiple models of pneumatic and electric high-shear dispersers. Our popular electric models include two options for controlling speed: mechanical hand knob or electronic variable frequency drive (VFD).
For a detailed description of each, please reference the relevant owner’s manuals. The following is intended to walk you through the process of operating a variable speed electric disperser for the most successful result from your dispersion application.
Step 1: Preparation
- Ensure you have all the necessary safety equipment, including goggles, gloves, and a lab coat.
- Verify that the benchtop disperser is securely positioned on its workstation and that the container holder is tightened to prevent rotation of the mixing vessel during operation.
- Safety Note: Never operate a high-speed dispersion blade in open air. The liquid in the vessel serves to dampen any vibration that may occur during operation.
Step 2: Air and Power Source Verification
- Ensure the disperser is powered by a reliable power source for the specified voltage and current - and that the power cord is out of the operator’s way. If the disperser features an explosion-proof motor, verify that electric connection has been completed by a licensed electrician following all relevant electrical codes.
- Verify that the pneumatic cylinder used to raise and lower the mixer head is supplied with a suitable compressed air source equipped with a filter-regulator-lubricator upline from the mixer.
- Check that the cylinder is primed by first moving the control valve lever down to “charge” the cylinder then test vertical movement by slowly lifting the control valve lever.
Step 3: Submerge the Disperser Shaft
- Lower the disperser shaft into the liquid medium in the vessel. Ensure the impeller is fully submerged.
- The dispersion blade should be approximately 1/3 the container diameter and positioned one blade diameter off the bottom. At a minimum, there should be as much fluid above the blade as below during operation.
Step 4: Mixing Process
The dispersion process works by bringing the blade to a high rate of speed in the base liquid medium then quickly adding the materials to be dispersed. This ensures they are contacted by the blade multiple times and affected by the high shear rapidly before the batch viscosity dramatically increases.
- Start the disperser motor at low speed in the base material.
- Increase motor speed until a deep vortex is formed – the top of the blade where it joins the shaft should be visible from above.
- Rapidly add dispersed materials into the vortex and observe its distribution and the change in the mixture.
- Speed may be increased to maintain a vortex while adding contents as needed until finished.
- The vertical positioning of the blade may also be adjusted for some dispersions as required.
- Note: The above steps describe a “baseline” process for achieving rapid dispersions. INDCO recognizes that there are many alternative and unique processes that may suit an individual application.
Step 5: Cleaning and Maintenance
- Once the dispersion process is complete, power off the disperser and remove the shaft from the liquid medium.
- Thoroughly clean the disperser shaft, blade, and vessel using appropriate cleaning agents. Clean any residual materials that may be on the frame or mixer drive head.
- Perform routine maintenance to ensure the disperser's longevity and optimal performance.
Applications of High-Speed Dispersers
High-speed dispersers have applications in various industries due to their versatility and effectiveness. Some common applications include:
- Paints and Coatings: Achieving optimal pigment dispersion and color development.
- Chemicals: Ensuring thorough mixing and blending of chemical compounds.
- Adhesives and Sealants: Creating consistent and high-quality adhesive formulations.
- Pharmaceuticals: Efficiently dispersing active ingredients in drug formulations.
- Cosmetics and Personal Care: Homogenizing and emulsifying cosmetic products for optimal texture and stability.
Contact INDCO For Help
We hope this guide has provided you with valuable insights and answered your questions about dispersers. Remember to follow safety precautions, refer to the manufacturer's instructions, and practice proper maintenance for the disperser's optimal performance. If you have any further inquiries or require assistance, feel free to contact the INDCO team. Happy dispersing!
Other blogs related to dispersion:
Fundamentals of Dispersion in Mixing